2009年8月21日 - クランクケース内の強制減圧(その3) 経路中にリードバルブを設置 |
 |  |  |  |  |
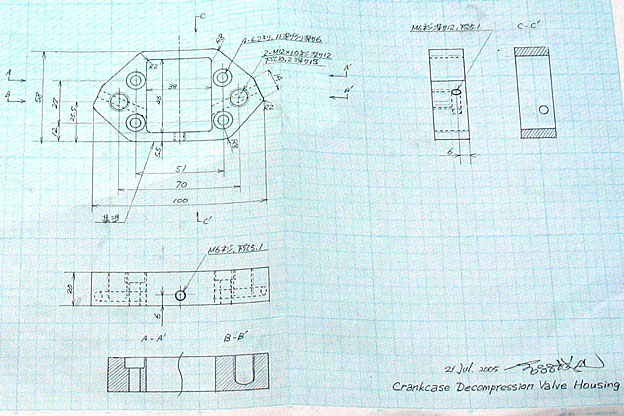 |
吸気負圧だろうが排気負圧だろうが、運転状況によって変動する負圧を利用してクランクケース内を強制減圧する場合、途中に逆止弁(ワンウェイバルブ)が必要である。これがなければ、吸気負圧や排気負圧がクランクケース内圧よりも高くなったときに逆流する。それではクランクケース内圧を低めに保つこはできず、強制的に減圧する意味がない。 |
| あのYZR-M1だって、排気ポート直後から導かれた負圧ホースがクランクケースに入るところにリードバルブを備えているから、これの設置は最初から必須だと考えていた。 で、リードバルブには、値段が安くて入手が容易なヤマハ・ミントの物を使うことにして、その実物を採寸し、リードバルブを収納するハウジング(吸気ホースとブリーザーホ |
| ースのコネクター)を設計した。 こういった、参考例がない物を作る場合は机上検討が欠かせない。何枚もラフを描き、だいたいの形が決まったところで、製作者である自分に製造を依頼するつもりで上の図を描いた。旋盤でひいて終わり…とは異なり、いくつもの加工が必要な場合、段取りを考え、ミスをなくすために、正確な図面は欠かせない。 | |
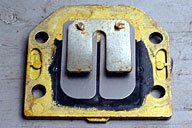 |
| 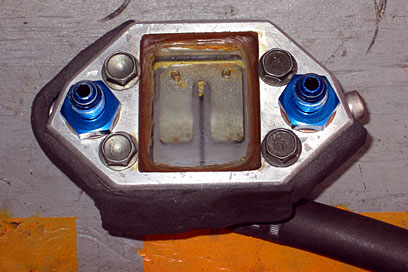 |
|
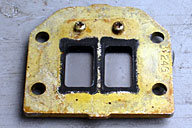 |
制作に当たって最も時間がかかったのは、覗き窓のガラスを入れる穴加工だ。グローリーホールに行ってボール盤を借り、φ4〜5mmの丸穴を無数に開けて窓の中身を取り除き、その後6時間ほどヤスリをかけまくって、ようやく窓枠が完成。続いて各種の穴あけをし、メネジ加工が必要な箇所にはタップをたて、丸一日かかってようやく本体が出来た。 |
| 窓ガラスが奥に入り込まないようにする位置決めは、フライス盤+エンドミル加工ができないので、厚さ1mmのアルミの帯板を曲げて嵌め込んだ。ガラス板は、専門家(グローリーホールのお客さん)にお願いして+0.5mm程度の寸法に切り出してもらい、専用の砥石(水で濡らして使う)で窓枠ぴったりに仕上げた。 ガラスとアルミのに接着は水上化 |
| 学工業所の接着相談室を参考に、信越化学のKE45を使用した。動かないようにくっつけるというよりはシールが主目的だから、適剤である。 その他、これを作るために、行き止まり穴用スパイラルタップや、中心に近い部分を除きエンドミル的な穴あけのできる武蔵ドリルというキリなど、それまで知らなかったツールを知り、使えたのも収穫だった。 | |
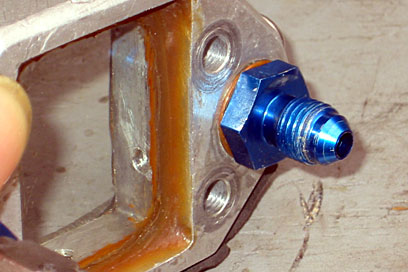 |
| 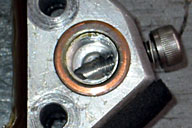 |
|
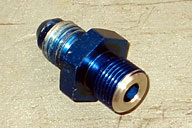 |
本体に時間がかかった(体力と手のひらの皮も消耗した)ので、本体と同じくらい凝った造りになるはずの裏ブタは、結局計画だおれに終わり、うまい具合に66ナイロン製のエルボーという便利な物を見つけたので、思い切り簡略化をし、5mm厚のアルミ板をコンター(帯鋸盤)で切り、ボール盤で穴を開け、タップをたてるだけにして完成を急いだ。 |
| 66ナイロンとアルミ板の接着は、セメダインの接着相談室に電話で確認し、問題ありません…と言われた同社のEP001を使用。製作から4年経過した今も、割れ/剥がれ/侵食などによるリークはなさそうだ。 シリンダー両脇のY.I.C.S.連通通路端の負圧取り出し口に接続する2本のホースには、アールズの3番を使用。テフロンチューブ+ステンレ |
| スメッシュ被覆の、オートバイの油圧ブレーキに使われているのより1サイズ太い物である。 クランクケースブリーザーとの接続には、普通のゴムホースを使用。左クランクケースカバー上部で90度近く曲がる部分には、中に金属製コイルスプリングを入れて“折れ”を防止し、接続部は1箇所あたりタイラップ3本がけで固定している。 | |
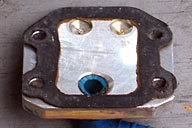 |
| 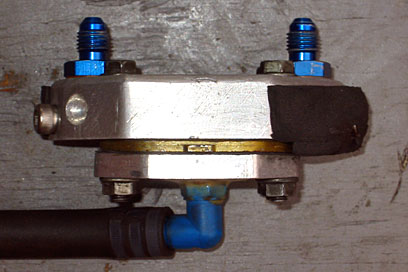 |
|
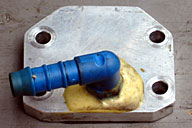 |
|