2011年11月12〜13日 - クラッチスプリングの偏心を防ぐリテーナーを製作して装着 |
 |  |  |  |  |
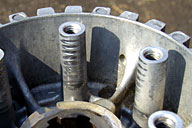 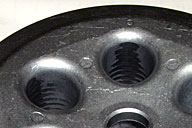 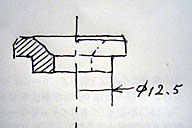 |
クラッチスプリングの傾き(端部の偏心)や捻れによる、上の写真のような接触痕。 これは、私のXJ900に限らず、この部分にコイルスプリングを用いたストリートバイクにはごく普通に見られる現象である。 大した問題ではない…と言ってしまえばそれまでだし、これが原因で大きなトラブルが生じることも、たぶんないだろう。だが、凸凹の面に接触しつつスプリングが伸縮するのだから、動きがいいわけがない。 これを何とかするには、いろんな方法がある。2007年9月〜2008年2月のエンジンオーバーホールに合わせ |
| て私がした、クラッチボスの突起の外周にテフロンチューブを巻くというのもそのひとつ。以後3万km以上の走行で耐久性に問題がないのは確認できたし、少なくともクラッチボス側には(接触はしているが)傷をつけない状態を保っている。 ところが、わずかとはいえ、プレ ッシャープレートの穴の内壁にも新しい接触痕が見つかり、こちら側も何とかしたいと思っていた。 いや、実は“何とかしたい”ではなく“スプリングの内径にぴったりの出っ張りを持った段付きワッシャを作ってクラッチスプリングの偏心 |
| を防ごう”と、ずっと考えていた。 ヒントはワークスマシンである。1986〜87年に触るチャンスのあったYZR250(OW82〜85)のクラッチスプリングスクリューは、今回私が作ったワッシャとボルトを一体化したような形状の、アルミ削り出しの専用パーツで、頭の下側に設けられた突起がクラッチスプリングの内側にピタリと嵌まり、偏心を防いでいた。 市販レーサーTZはそうではなく、XJ900と同じく、 ただの平ワッシャだけで押さえる構造(偏心する)だ ったから、さすがはワークスマシン …と感心したものである。 |
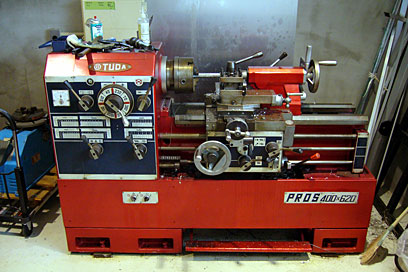 |
| 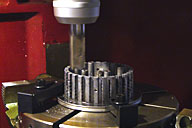 |
|
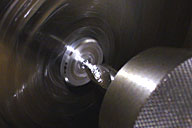 |
入手以来10万kmを 超えるXJ900とのつきあいの中で、クラッチをバラした回数は数え切れない。組み立て時は常に、クラッチスプリングが偏心しないように最新の注意を払って取りつけていても、バラすときに偏心していないことはほとんどない。 接触痕が、クラッチボスは内側、プレッシャープレートは外側に顕著なことからして、スプリングが偏心するのは、ねじれ+遠心力のしわざと考えてよさそうである。 以前からずっと考えていた偏心防止策を、この期に及んで施そうと決断したのは、ここ最近のメンテナン |
| スとチューニングを通じて、自分の中でクラッチへの関心が高まっていたのと、まったくうまいタイミングで、自由に使える旋盤とフライス盤を見つけてしまったからだ(笑)。 ここの工作室の主は、私のオートバイ整備の師匠である。もう、かれこれ30年以上のつきあいの中で、整備の基礎から旋盤の使い方に至るまで、教えてもらったことは数え切れない。師匠が京都市内でオートバイ屋さんをしていたときは、そこにあ った(今回のより、もっと小さな)旋盤を使って、当時私がメカニックをしていた 三浦昇のTZ250用パーツ |
| を作らせてもらったものだ。 アルミに置き換えて大丈夫な、そこそこの精度で問題のない円筒状または円盤状のパーツはほとんど自作し、スズキの市販レーサーRG系の軽量ネジ類と合わせ、とにかく、ヒマさえあれば軽量化を進めていた。おかげで、出場車中一二を争う軽量なマシンにすることができた。 今の私が、自分のバイクの軽量化に関心がないふうに装っているのは(笑)、これをやり出すと本当にキリがなくなるのと、少しくらい速くはなるかもしれないが、気持ちよくなるかどうかは疑問だからだ。 |
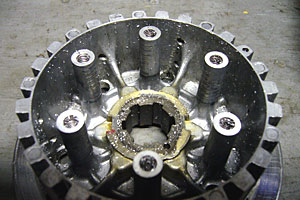 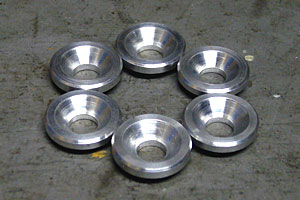 |
話をもとに戻すと、師匠の工作室に旋盤しかなかったら、この計画はまたしても先送りになっていたはずだ。となりにフライス盤があり、ワ ッシャの製作とクラッチボスの加工が一度に済む…という、メンドクサがりの私にぴったりの環境を揃えてくれた師匠に感謝である(笑)。 材料は、 ISAに新しいスプロケットの写真を撮りに行った(私が同社のウェブマスターなので)ついでに社長に「17パイ以上のアルミの丸棒の端材、余ってへんやろか?」と尋ねたら「17かぁ…、25で良かったらもう使わへん2014のが余っとるから |
| 1本あげるわ。そこのカッターで適当な長さに切ったら、バイクに積んで帰れるやん」と、うまい具合に話がまとまり、1本頂戴した。 で、12日は、その材料とクラッチボスを持って師匠の工作室へ行き、“こんなのを作りたい…”と、絵を描きつつ、自分なりに考えた“段取り”を説明した。“外径を削る→端面を仕上げる→面取りをする→中穴を開ける→サラモミをする→小径部の外径を削る→必要な長さを残して小径部で突っ切る”というのが私の案。1個作る間に一度もつかみ直す必要がないので、そうしたかった。 |
| ところが師匠は「突っ切りではキレイな面が出えへんから、一番大事なクラッチボスとの当り面は、突っ切りで済まさんと、ちゃんと仕上げたほうがええ」という理由で“外径を削る→端面を仕上げる→小径部の外径を必要な長さだけ削る(段差を作る)→大径部を(仕上げの余裕を見て)突っ切る→裏返しにして(段差をくわえて)表面を仕上げる→面取りをする→中穴を開ける→サラモミをする”という修正案を提示。 言い終わるが早いか、師匠は丸棒をくわえて端面を仕上げ、そこから2.5mmのところまでø12.5に外径を加 |
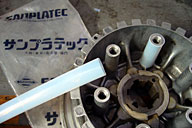 |
| 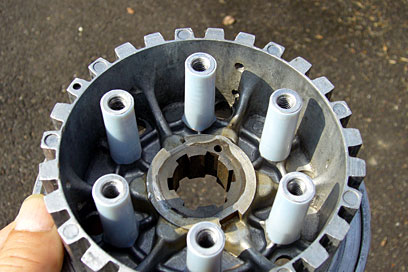 |
|
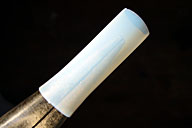 |
工し、適当なところで突っ切って裏返しにチャックにくわえて「ほれ、2.5mmあったら くわえられるやろ」と言いながら、突っ切った面の仕上げにかかり「ほれ、突っ切りでは、ちゃんと面が出てへんやろ」と、どちらも実演し、現物を見せながら説明し、納得させてくれた。 30数年前、オートバイのメカに興味を持ちはじめた私に整備の基礎を教えてくれたときと変わらぬやり方である。まったく素晴らしい人と出会ったものだ…と、師匠に感謝するとともに、自分の運の良さを感じつつ、師匠案に従って作業を始めた。 |
| ところが、削れども削れども、丸棒はなかなか細くならない(笑)。欲張って、必要以上に外径仕上げの長さを長くしすぎた(この時点では12個作るつもりだった)ので、なおさらだ。最初から6個のつもりにしとけば、少なくとも、削っている時間は半分で済む…と気づいたときにはしかし、 ø20程度にはなっており、あと少しなのでそのままいった。 師匠が戻ってきて「まだ外径だけかいな…。 ISAにあるような高速加工機やったらすぐやのになあ(笑)。まあ、晩メシまでには終わるつもりで、ゆっくりやったらええわ」と言 |
| いながら、隣のフライス盤にロータリーテーブルをセットし、その上にクラッチボスを固定してしまった。 「面の傾きとか荒れとかを軽う平して、そこから 2.5mm削ってもええんかいな?」と聞かれて「うん、それでええわ」と返事をすると、師匠はすぐに作業を始め、私がワッシャを1個作るよりも短い時間で6本の突起を全部削り落としてくれた。 この間、かろうじて写真を1枚撮 ったのみで、作業手順をよく観察できなかったのが心残りである。が、まあ、この師弟コンビだから、次には自分でできそうな気がする(笑)。 |
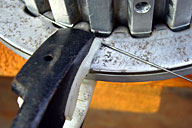 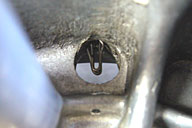 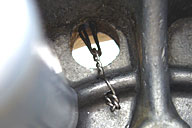 |
クラッチボスの加工を終えた師匠は、電源の落とし方と戸締まりのしかたを私に教え、再びどこか(本来の仕事場?)へ行ってしまった。これにより、プレッシャーが少々軽減された私は(笑)、残る5個のワッシ ャを、自分のペースで製作できた。 同じ物を何個も作るのは面倒なので、師匠案をベースに、できるだけ手順を簡略化した。ノギスで測りながら削ったのは大径部の外径のみ。小径部の外径や、大径部/小径部それぞれの長さ(厚さ)は、前の工程が終わったときのバイトの位置を基準に、送りネジの目盛りを頼りに決 |
| めた。ザグリの深さは(皿ボルトを嵌めてみての)現物合わせだし、面取りに至っては、ほぼ45度に傾けたバイトを向こう側の角に当て、ワークを逆転させながらバイトを手前に送る…という超手抜き(笑)。面取りの幅は、得意の“見た目”が同じになるように揃えただけである。 まあ、その程度の物だからこそ、自分で作る気になったわけで、クォリティはもともと追求していない。このワッシャの場合は“ちゃんとできていること”よりも“これを装着していること”が重要なのだ(笑)。 とはいえ、せっかく作ったパーツ |
| なのだから、最後の仕上げはきちんとしておきたい…というわけで、翌13日に、クラッチボスとの当り面に軽くオイルストーンをかけた後、すべての角に糸面取りをした。 ちなみに、 中穴径は6.5mmと大きめで、皿ボルトの首下にある隅Rをクリアしている。う〜む、本当は皿ボルトじゃないほうが良かったし、同じ皿ボルトでも、せめて黒染めのTORXくらいは使いたかったなあ…などと考えつつ、ここはしばらくこのままで、もう1件クラッチ関連の改善を図りたい。補修部品の揃ったリアショックは、その次あたりか…。 |
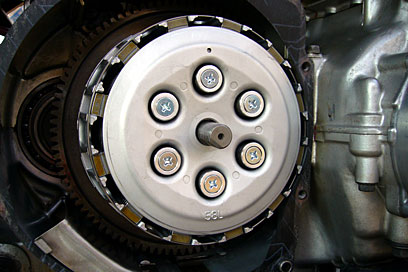 |
| 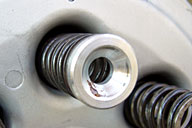 |
|
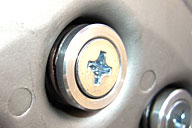 |
|