2011年11月16〜19日 - クラッチハウジングとプライマリードリブンギアの結合方式を変更 |
 |  |  |  |  |
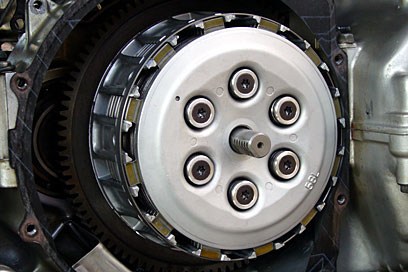 |
| 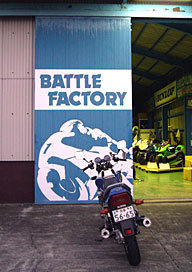 |
12日に作り、13日に装着した“クラッチスプリングの偏心防止用ワッシャ”は、その後、師匠に「ホームセンタークォリティやなあ」と言われたユニクロメッキの+ネジの代わりに、ネット通販で入手した(14本という小ロットで購入できた)黒染めのTORXネジで装着し、完成した。 だが、クラッチにはもう1箇所、忘れてしまわないうちに手を加えておきたいところがあった。10月20日 に組み立てたばかりのプライマリードリブンギアコンプリート(プライマリードリブンギア+クラッチハウジング)に採用したボルト+ナット |
| を溶接するという手法を、ボルト+ナットをネジロック剤+ロックワッシャで留めるという、より安心な手法に改めておきたかったのだ。 大きな力に耐えるための強度を考えれば、これは改善ではなく改悪である。しかし、もとがリベット留めなことからもわかるように、引っ張り応力はほとんどかからず、剪断応力も大して大きくない。しかし、小さいとはいえ、反復する荷重が繰り返しかかるから、ここで優先すべきは、強度よりも耐久性、材料で言えば硬さよりも粘り強さなのではないか…というのが変更の動機である。 |
| もとのリベットの材料は、SV41というリベット専用の合金鋼であるらしく、強度はSS41相当、つまり、ボルトの最小引張荷重4Tあたりの、け っこうナマクラな物だ。それを、焼いたり溶かしたりせずにリベッティングしているから、完成した状態でもナマクラのままである。 これに対して、私の10月20日仕様では、ボルトの強度区分が12.8、ナ ットは不明。そこに溶接による焼きが入っているから、溶接箇所とその周辺は、リベットと比べて相当に硬く、それだけならいいが、合わせて脆くもなっていると想像できる。 |
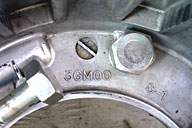 |
| 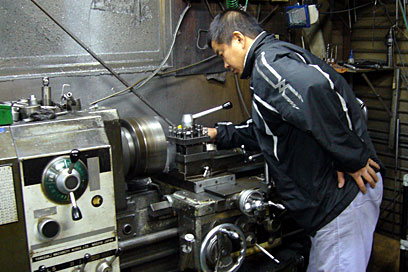 |
|
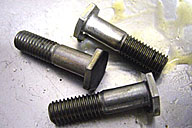 |
そこでまず、溶接以外の、ナットの緩み止め&脱落防止策を考えた。緩み止めと脱落防止は似て非なるものだし、緩みの中にも回転を伴う緩みと回転を伴わない緩みがある。こうやって整理してみると、回転を伴わない緩みについては、もともと大して締まっていない(軸力を発生していない)のだから考えなくてもよさそうだ。そこで、回転しないようにすることと、例え少しくらい回転しても脱落しないようにすることに狙いを絞って設計を進めた。 ついでに、せっかくやり直すのだから、ボルトも、前作のような強度 |
| 区分12.8の硬いヤツではなく、もうちょっとナマクラなのにしたい。 で、ナットの回り止めには、ボルトにもナットにも熱を加えたり変形を与えたりすることなく施工できるネジロック剤を用い、万一それが効かなくなっても脱落しない(緩み回転が進まない)ように、ロックワッシャを併用することにした。 ただ、ボルト+ナット止めの箇所で、ナットにだけロックワッシャを使っても無意味なので、ボルト側にも回り止めをしなければならない。それも、できるだけクラッチハウジングには手を加えずに実現したい。 |
| こうした諸々の条件を満たすべく最初に探したのは、M8/円筒部の長さ15mm/頭の二面幅14mmのボルトだ った。これら3つの条件のうち、ネ ックになったのは3つ目である。M8ボルトの二面幅といえば12mmか13mmに決まっており、14mmなどというのは規格品ではない。そのため、ネット通販では入手不能。純正部品で何かなかったかな…と、古い記憶を探 ってみて、 TZ250のドリブンスプロケットを留めるのに使われていたボルトが、M8で二面幅14mmだったことを思い出した。円筒部の長さも、ち ょうどよさそうな感じである。 |
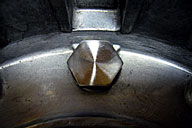 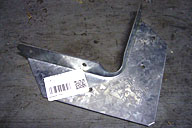 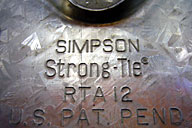 |
1981年型(5F7)以後数年のTZ250は、70年代の1H3/1H4あたりと同じリアハブを使っており、ワイド化したリアタイヤを避けるべくオフセットの大きくなったチェーンラインに合わせ、スプロケットの裏側に10mm厚のスペーサーを入れ、それとスプロケットを共締めしていたのだ。 さっそく例のサイトに行き、1981年型TZ250Hのパーツリストでリアホイールのページを見ると、このボルトの品番は 90109-08618と判明。急いで某オートバイショップに3本注文し、翌々日に現物を入手した。 届いたボルトは、まるで誂えたよ |
| うに、六角頭の1辺がクラッチハウジングの縁に接触して回り止めとして機能し、円筒部の長さも、 6mmのクラッチハウジング+ 6mmのカラー +2.5mmの裏板+1mmのロックワッシ ャの合計15.5mmを締めつけるのに最適の寸法(不完全ネジ部を含めて、ちょうど15mm)だった。 前作では、六角穴付きボルトを用い、頭をサンダーで削っていたが、熱を加えないのが今回のテーマのひとつなので、サンダーではなく旋盤で加工したいところ。再び師匠に借りようかな…と思っていたら、うまい具合に鈴鹿に行く用事ができた。 |
| レース関連ショップが集まる鈴鹿に、 このボルトの頭を2.5mmに削り落としてくれるところがないはずがない(笑)。だが、昔とは異なり、今の私は鈴鹿の事情に疎い。そこで、オートバイのメカと鈴鹿の事情に詳しい2人の知人に電話で尋ねてみたところ、異口同音に「そりゃあバトルさんでしょう」との回答が…。 そんなわけで、鈴鹿サーキットでの用事を済ませた私は、昔から知ってはいたが訪れたことのなかったバトルファクトリーさんを訪ね、Tさんに旋盤加工をしてもらった。その場で、30年ぶりくらいにKさんとも |
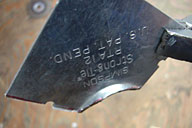 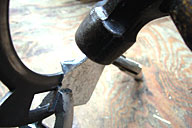 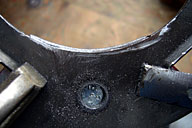 |
再会でき、お互いに元気なのを確認しあえたのも嬉しかった。 こうして、バトルファクトリーの社長や、社長に話を通してくださった“キャブ仙人”こと永冶さんを含む多くの方々のご厚意に支えられ、スペシャルボルトは完成した。みなさん、ありがとうございます。 ボルトの次はロックワッシャである。どう考えても、コイツは板材から自分で切り出すしか方法はなさそうだ。その板材探しがまた大変だった。アルミ、ステンレス、銅、真鍮などの板材はあるのに、鉄板はホームセンターになく、かといって材料 |
| ショップで買うには、あまりにも最小販売サイズが大きすぎる。 そこで“ほんまにちょっとでええねん”から、材料ではなく、鉄板を使った何がしかの部品から切り出すのがよさそう…と考えを改め、ホームセンターを隅々まで探して見つけたのが“ストロング・タイ”という名の、建築用の隅金具だった。 1個157円のそれを3個買い、 どういうふうに使うか検討した。その結果、角の内側にある“返り”の部分を生かし、そのRを大きくしつつ両側に広げていく感じで板金加工をした後にボルト穴を開け、あとで必要 |
| な形に切り抜くことに決めた。 ロックワッシャなんかを作るのは初めてだから(笑)、考えたとおりにできるかどうか心配しつつやってみると、思ったよりもはるかに簡単だ った。それはもちろん、精度も仕上げも追求していないからではあるのだが、とりあえず1個作り終えた段階で、あと2個作る気力が残っていたのには自分でも驚いた(笑)。 最難関のロックワッシャができてしまえば、あとはこっちのもの。ボルト、ナット、ロックワッシャを仮組みし、軸力が発生せず、かつ、ガタが生じない程度の力でナットを締 |
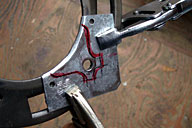 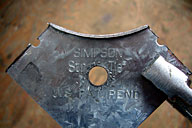 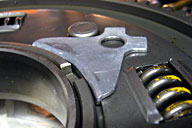 |
めつけ、その状態でナット表面とボルト端面の高さが 裏板から4.5mmになるように削ればいいだけだ。 前作では、この加工に、何の疑問も感じずにサンダーを使った。しかし今回は“熱を加えない”がテーマだから、 1.2mm厚のロックワッシャと6mm厚のナットの合計高さを4.7mm程度まで落とす工程にのみサンダーを用い、あとはヤスリとサンドペーパーだけで4.5mmに仕上げた。 そのサンダーがけも、一気にせず、少し削っては隣に移り、 3箇所を順番に回りつつ徐々に薄くしていくなど、徹底して“焼け”防止を図った。 |
| ナット表面とボルト端面の追い込みが終わったところで、いったん分解し、ボルトの先端とナットの内外周に面取りを施すとともに、すべてのパーツをバラして切削粉を洗浄。次はいよいよ“本締め”だ。 まずは、ロックタイトを塗らずに(ドライで)ナットをかけ、1箇所につき数回、締め〜緩めを繰り返しながら、3点の被締結パーツ(ハウジング/スペーサー/裏板)を隙間なく固定し、しかし軸力が立ち上がらないポイントを探る。そして、3箇所とも締まった状態にしてから、1箇所ずつ緩め、ロックタイトを塗 |
| り、もとの位置までナットを締め込めば締結そのものは完了である。 あとはロックワッシャの爪を起こし、長すぎる部分をカットするだけだ。曲げ(伸ばし)による疲労破断をテストして、9回連続で曲げ〜伸ばしをすると千切れる材料だから、曲げ〜伸ばし〜曲げ程度には充分耐えるはずだ。だから、一度曲げてカ ットし、伸ばしてからナットを締めつけ、再び曲げるという手順も考えたが、できるだけ強度低下を避けるべく、曲げは一度にし、最後にカット(実際にはヤスリで削り落としただけ)し、無事に全作業を終えた。 |
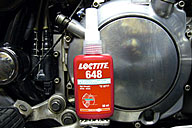 |
| 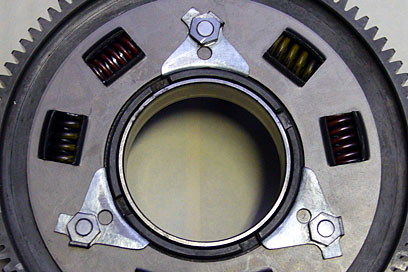 |
|
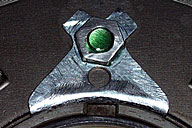 |
|